INHALE is a cultural platform where artists are presented, where great projects are given credit and readers find inspiration. Think about Inhale as if it were a map: we can help you discover which are the must-see events all over the world, what is happening now in the artistic and cultural world as well as guide you through the latest designers’ products. Inhale interconnects domains that you are interested in, so that you will know all the events, places, galleries, studios that are a must-see. We have a 360 degree overview on art and culture and a passion to share.
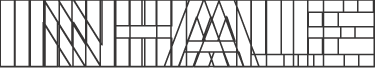
Nervous System is a design studio that works at the intersection of science, art, and technology. We create using a novel process that employs computer simulation to generate designs and digital fabrication to realize products. Drawing inspiration from natural phenomena, we write computer programs mimicking processes and patterns found in nature and use those programs to create unique and affordable art, jewelry, and housewares.
Kinematics is a system for 4D printing that creates complex, foldable forms composed of articulated modules. The system provides a way to turn any three-dimensional shape into a flexible structure using 3D printing. Kinematics combines computational geometry techniques with rigid body physics and customization. Practically, Kinematics allows us to take large objects and compress them down for 3D printing through simulation. It also enables the production of intricately patterned wearables that conform flexibly to the body.
Kinematics is a branch of mechanics that describes the motion of objects, often described as the “geometry of motion.” We use the term Kinematics to allude to the core of the project, the use of simulation to model the movement of complex assemblages of jointed parts.
Today we are releasing a jewelry collection and an accompanying customization app built upon our Kinematics concept. We’re also releasing a free to use app for desktop 3D printers.
Kinematics produces designs composed of 10’s to 1000’s of unique components that interlock to construct dynamic, mechanical structures. Each component is rigid, but in aggregate they behave as a continuous fabric. Though made of many distinct pieces, these designs require no assembly. Instead the hinge mechanisms are 3D printed in-place and work straight out of the machine.
Concurrently with the development of the online applications, they’ve been working on a more advanced software with broader practical applications. Kinematics allows us to design a shape and then fold it into a more compressed form for 3D printing. Items we’ve created so far are flexible, but rigid objects could be created by introducing a hinge joint that locks at a preferred angle. Here we present an example of how Kinematics can be used to create a flexible dress that can be printed in one piece.
The process begins with a 3D scan of the client. This produces an accurate 3D model of the body upon which we draw the form of the desired dress. For this example, the top of the dress conforms exactly to the torso, but the skirt has a larger silhouette, allowing for the dress to drape and flow as the wearer moves.
The surface of the sketched dress is then tessellated with a pattern of triangles. The size of the triangles can be customized by the designer to produce different aesthetic effects as well as different qualities of movement in the dress (the smaller the triangle, the more flexible the structure / the more fabric like it behaves). Next we generate the kinematics structure from the tessellation. Each triangle becomes a panel connected to its neighbors by hinges. The designer can apply different module styles to these panels to create further aesthetic effects.
Finally, we compress the design via simulation so it fits into a 3D printer. This means that an entire gown, much larger than the printer itself, can be produced in a single assembled piece. The simulation uses rigid body physics to accurately model the folding behavior of the design’s nearly 3,000 unique, interconnected parts and find a configuration that fits inside the volume of the printer.
text by n-e-r-v-o-u-s.com